In hohen - Geschwindigkeitskommunikationssystemen ist elektromagnetische Interferenzen (EMI) eine der wichtigsten Herausforderungen, die die Signalintegrität und die Gerätestabilität beeinflussen. Als Kernträger der optischen Module bestimmt das Abschirmdesign des SFP -Käfers (kleiner Form - Faktor) seine Anti -- -Interferenzfähigkeit direkt. Insbesondere in Szenarien mit hoher Frequenzanwendung wie 5G und Rechenzentren hat die Optimierung der EMI -Abschirmleistung des SFP -Käfigs eine oberste Priorität für die Gestaltung von Kommunikationsanschlüssen geworden.
01 Warum braucht der SFP -Käfig Präzisionsumschlag?Als Schnittstelle zwischen dem optischen Modul und dem Motherboard des Geräts muss der SFP -Käfig zwei Arten von Interferenzrisiken während der hohen - Frequenzsignalübertragung behandeln:
1.
Interne Einmischung: Die vom optischen Modul erzeugten elektromagnetischen Wellen beim Arbeiten durch die Käfiglücken und stören andere Komponenten;
2.
Externe Einmischung: Externes elektromagnetisches Rauschen dringt durch die Grenzfläche ein, was zu einer Erhöhung der Signalbitfehlerrate führt.
Wenn die Abschirmwirksamkeit nicht ausreicht, kann dies bestenfalls eine Signalschwächung verursachen oder sogar Systemausfallzeiten verursachen. Gemäß dem Standard -Standard der IEC 61967 muss die Kommunikationsgeräte den Strahlemissionstest im 30 -MHz -Frequenzband bestehen, der strenge Anforderungen an das Abschirmdesign des SFP -Käfigs stellt.
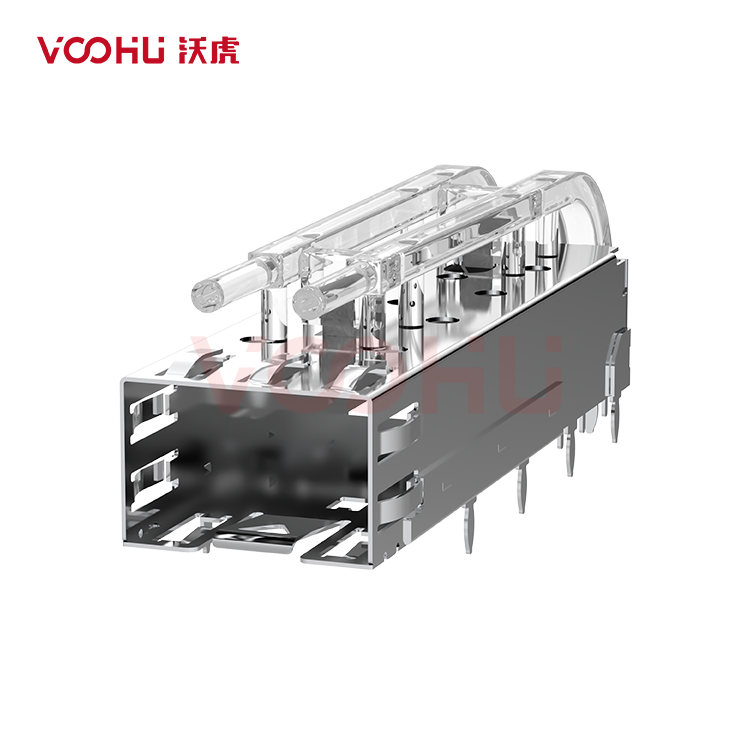
02 Fünf Kernelemente des SFP -Käfig -EMI -Abschirmungsdesigns1. Auswahl hoher LeitfähigkeitsmaterialienBasismaterial besteht vorzugsweise aus Metallen mit hoher Leitfähigkeit wie Edelstahl (SUS304) oder Beryllium Kupfer (C17200), um sicherzustellen, dass elektromagnetische Wellen auf der Oberfläche des Schildes Wirbelstromverluste bilden.
Oberflächenbehandlung: Goldbeschichtung (0,1 - 0,2 μm) oder Nickelbeschichtung (3 - 5 & mgr; m), um die Kontaktimpedanz zu reduzieren und die Effektivität der Häufigkeit der Frequenz (SE -≥ 60 dB@1 GHz) zu verbessern.
2. Integriertes vollständig geschlossenes Strukturdesign integriertLochgrößenregelung: Wärmeableitungslöcher und Montagelöcher müssen dem λ/20 -Prinzip folgen (Apertur <1/20 der höchsten Frequenzwellenlänge). Beispielsweise muss die Blende, die 6 GHz entspricht, weniger als 2,5 mm sein;
Versiegelung der Abschirmabdeckung: Nahtloses Crimping zwischen der Abdeckung und dem Käfig wird durch Federblätter oder leitfähigen Schaum erzielt, und die Spaltbreite wird innerhalb von 0,1 mm gesteuert.
3. Multi - Punkt Erdungs und niedrige ImpedanzwegeFederkontaktdesign: Elastische Kontaktpunkte (≥ 4 Punkte/Oberfläche) werden auf beiden Seiten des Käfigs eingestellt, um eine zuverlässige Verbindung zur PCB -Bodenschicht (Kontaktwiderstand <10mΩ) zu gewährleisten.
Optimierung der Bodenbelastung: Verwenden Sie ein "Brunnen" - geformtes oder gittergeformtes Pad -Layout, um den Bodenpfad zu verkürzen und die Returnimpedanz zu verringern.
4.Vorgender HohlraumresonanzeffektStruktursimulationsunterstützung: Verwenden Sie ANSYS HFSS oder CST -Software, um die Hohlraumresonanzfrequenz zu simulieren, die Länge - zu - Breitenverhältnis des Käfigs anzupassen und das Betriebsfrequenzband (z. B. 3,5 GHz für 5 g) zu vermeiden.
Absorptionsmaterialfüllung: Ferritbeschichtung wird auf nicht - kritische Bereiche angewendet, um in bestimmten Frequenzbändern streunendelomagnetische Wellen absorbieren.
5. Balance zwischen Wärmeissipation und AbschirmungAuslegung der Richtungswärmeleitung: Fügen Sie ein thermisches leitendes Silikonpad auf der Innenseite der Abschirmabdeckung hinzu, um die Wärme zur Geräteschale zu lenken, um zu vermeiden, dass die Abschirmleistung aufgrund zu vieler Öffnungen geschwächt wird.
Material Composite -Technologie: Metall - Integrierte Formplatten (LDS -Technologie) werden verwendet, um Isoliermaterialien in lokale nicht geschützte Bereiche einzubetten, um die thermische Kopplungsstörungen zu verringern.
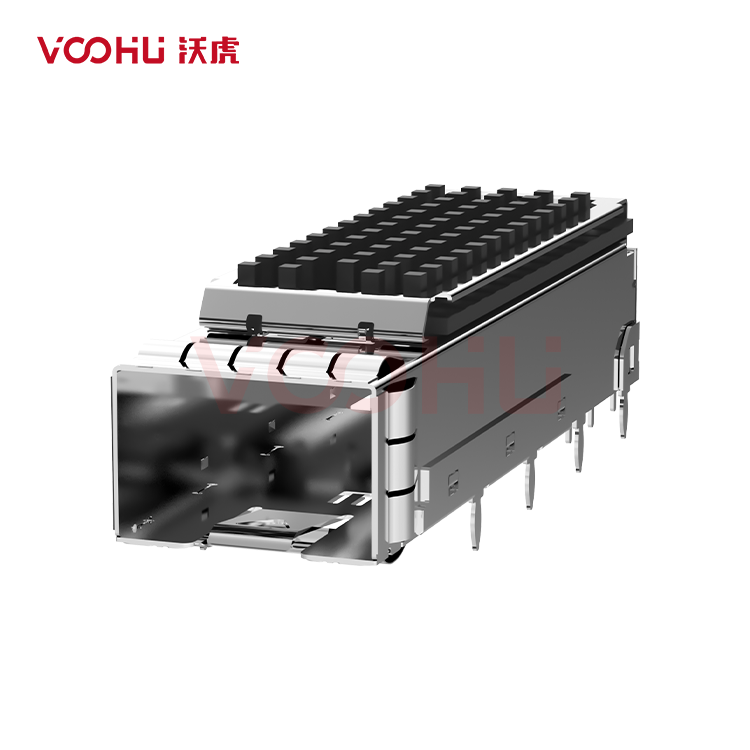
03 Branchentrends: zukünftige Innovationsrichtungen der Abschirmtechnologie1. Neue Verbundwerkstoffe: Graphenbeschichtungen und metallisierte Keramik im Ultra - Hochfrequenzband;
2. Intelligent Shielding: aktive Rauschunterdrückungstechnologie mit integrierten EMI -Sensoren;
3.Miniaturisierungsprozess: MIM -Prozess (Metallinjektionsformung), um eine komplexe Hohlraumstruktur zu erreichen.
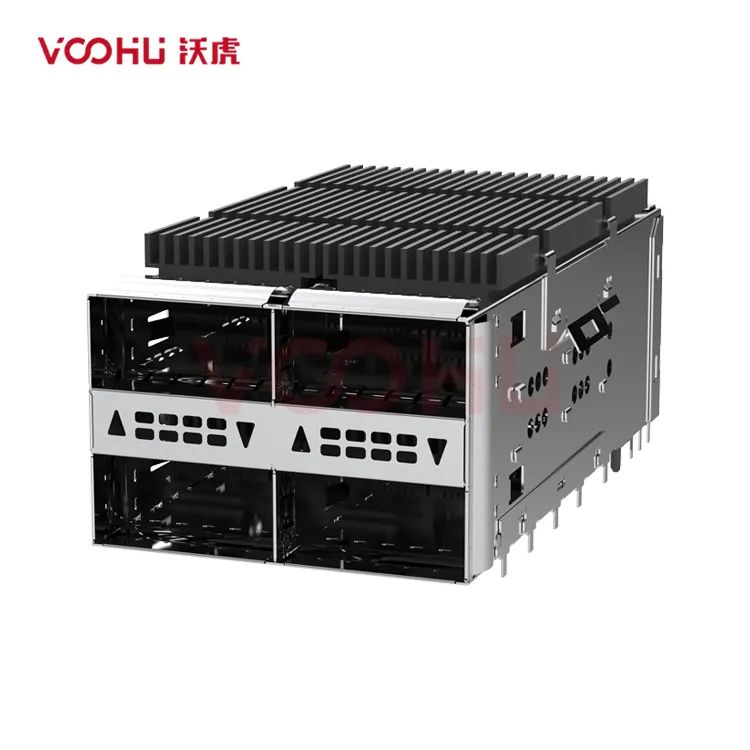
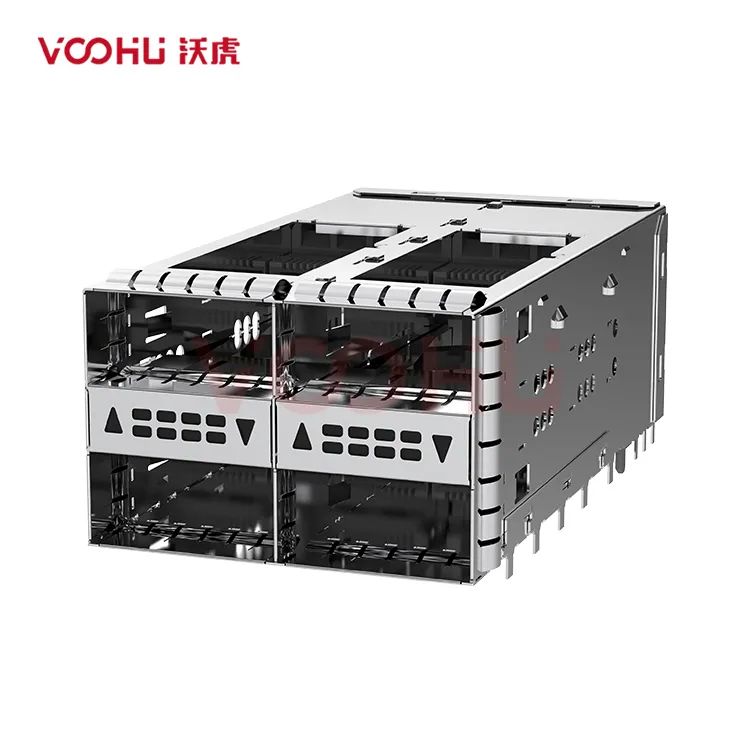
Folgen Sie [Voohu Electronics], um EMI -Testberichte und Proben zu erhalten!